At present, dry-mixed mortar is in a stage of rapid development. The use of dry-mixed mortar can effectively reduce resource consumption, improve project quality, and improve urban environment. However, there are still many quality problems in dry-mixed mortar. If it is not regulated, its advantages will be greatly reduced or even counterproductive. Only by strengthening quality control in various aspects such as raw materials, finished products, and construction sites, can the advantages and functions of dry-mixed mortar be truly brought into play.
Analysis on the common faults of dry-mixed mortar quality
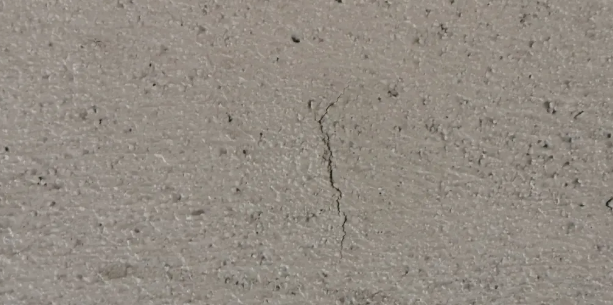
crack
There are four most common types of cracks: uneven settlement cracks in the base layer, temperature cracks, drying shrinkage cracks, and plastic shrinkage cracks.
Uneven settlement of the base
The uneven settlement of the base layer mainly refers to the cracking caused by the subsidence of the wall itself.
temperature crack
The change of temperature will cause thermal expansion and contraction of the material. When the temperature stress caused by temperature deformation under the constraint condition is large enough, thermal cracks will occur in the wall.
drying shrinkage cracks
Drying shrinkage cracks are referred to as drying shrinkage cracks. As the water content of masonry blocks such as aerated concrete blocks and fly ash blocks decreases, the materials will have large drying shrinkage deformation. The shrunk material will still expand after being wet, and the material will shrink again after dehydration.
Shaping shrinkage
The main reason for plastic shrinkage is that within a short period of time after the mortar is plastered, shrinkage stress is generated after the moisture is reduced in the plastic state. Once the shrinkage stress exceeds the bond strength of the mortar itself, cracks will occur on the surface of the structure. The plastic shrinkage on the surface of plastering mortar is affected by time, temperature, relative humidity and the water retention rate of the plastering mortar itself. In addition, negligence in design, failure to set up grids according to specifications, untargeted anti-crack measures, substandard material quality, poor construction quality, violation of design and construction regulations, failure of masonry strength to meet design requirements, and lack of experience are also Important reasons for wall cracks.
bulge
There are four main reasons for the hollowing: the surface of the base wall is not treated, the wall maintenance time is not enough to plaster, the single-layer plaster is too thick, and the plastering material is used improperly.
The surface of the base wall is not treated.
The dust adhering to the wall surface, the residual mortar and the release agent during pouring are not cleaned up, the smooth concrete surface is not painted with interface agent or sprayed, and the water is not fully wetted before plastering, etc., all will cause hollowing phenomenon.If the maintenance time of the wall is not enough, the wall is not fully deformed before plastering, and the shrinkage of the base layer and the plastering layer is inconsistent, resulting in hollowing.
Single layer plaster is too thick
When the flatness of the wall is not good or there are defects, it is not treated in advance. When plastering is eager to achieve success, it survives at one time. The plastering layer is too thick, causing its shrinkage stress to be greater than the bonding force of the mortar, resulting in hollowing.
Improper use of plastering materials
The strength of the plastering mortar does not match the strength of the base wall, and the shrinkage rate is too different, which is another reason for the hollowing.
Sand peeling off from wall
Measures to improve the quality of dry-mixed mortar
Raw material quality control
1. Cementitious material
The cementitious materials in dry-mixed mortar are mainly cement, gypsum and lime. The largest amount is currently cement, followed by gypsum. Cement is one of the basic raw materials in cement-based dry-mix mortar. The quality of cement has a great influence on the quality of construction projects. Therefore, strengthening the inspection of cement quality is of great significance to ensure the quality of construction projects.
The cement in the dry-mixed mortar should be made of general-purpose Portland cement, and bulk cement should be used, which should comply with the provisions of GB175-2007 “General-purpose Portland Cement”. Cement purchases should have quality certification documents. The main technical requirements of cement can be divided into two categories: chemical indicators and physical indicators. The laboratory mainly tests the physical indicators of cement.
2. Aggregate
The selection of aggregate should be analyzed from the aspects of mud content, stone powder content, particle gradation, harmful substances, firmness, bulk density, porosity, etc. Before the aggregate enters the factory, its particle gradation, mud block content, mud content must be analyzed. The amount, stone powder content and firmness are tested, and other items need to be checked by batch. Among them, in order to improve the strength of cement and mortar, it is necessary to use particles of different sizes for proportioning, that is, particle grading. The mud content refers to the content of particles with a nominal particle size of less than 80 μm in the sand, while the mud block content refers to the content of particles in the sand with a nominal particle size greater than 125 mm and less than 630 μm after washing or hand-kneading. If the mud content and mud block content in the sand are too large, it will affect the strength and durability of the mortar. Generally, the mud content should be controlled to be less than or equal to 3.0% and the mud block content to be less than or equal to 2.0%.
3. Admixtures
The admixtures used in mortar are divided into active fillers and inert fillers. Active fillers refer to fillers that have no or only weak hydration activity themselves, but can hydrate and produce strength in an alkaline environment or in the presence of sulfates. Commonly used active fillers are fly ash, granulated blast furnace slag powder, silica fume, zeolite powder, and steel slag powder. Inert fillers refer to materials that are inactive and cannot produce strength, such as ground quartz sand, limestone, hard slag and other materials, and their fineness is generally similar to or finer than cement. Adding inert fillers to mortar can reduce the amount of cementitious materials and reduce production costs. The admixtures used in the mortar should conform to their respective national and industry standards.
4. Additives
The amount of admixture used in dry-mix mortar is very small, but it can greatly improve the working performance of the mortar. Commonly used mortar admixtures are cellulose ether, redispersible latex powder, starch ether, water reducing agent, air-entraining agent, defoamer, anti-cracking fiber, etc. Different admixtures are selected for the modification of mortar in the production of different varieties of mortar.
5. Construction process control
When the plastering mortar is used, the thickness of each layer of plastering should not be greater than 10mm. When the plastering thickness is greater than 10mm, it should be plastered in layers, and the next layer of plastering should be carried out after the previous layer of mortar has solidified and hardened. Each layer of mortar should be compacted and smoothed separately, and the smoothing should be completed before setting. When the plaster thickness is greater than or equal to 35mm, strengthening measures should be taken, such as adding mesh cloth, steel mesh, etc. The mortar should be protected from quick drying, water washing, shock, vibration and freezing before setting. When the air temperature or the construction environment temperature is lower than 5 ℃, the dry-mixed mortar shall not be constructed without effective thermal insulation and anti-freezing measures.
6. Maintenance
After the construction of the mortar is completed and the surface layer is set, it must be moisturised and maintained in time to prevent early plastic cracking of the mortar, and the curing time of the mortar shall not be less than one week. In case of high temperature in summer, ensure that water is sprayed at least once every 4 hours during the day.